XHD-65/90/65-1850 is one of the most popular models among our customers and it is mainly used for producing:
1) stretch film rolls with below specs
* 2~5 KGS/roll small hand use stretch film rolls.
* 10~18 KGS/roll machine use stretch film rolls.
* Medium size rolls with roll weight around 33.5 KGS at 500 mm film width.
2) 8~10 microns 250~500 mm PE cling film rolls.
3) 30~35 microns 250 mm/300 mm/500 mm/750 mm silage film rolls (UV protective film rolls).
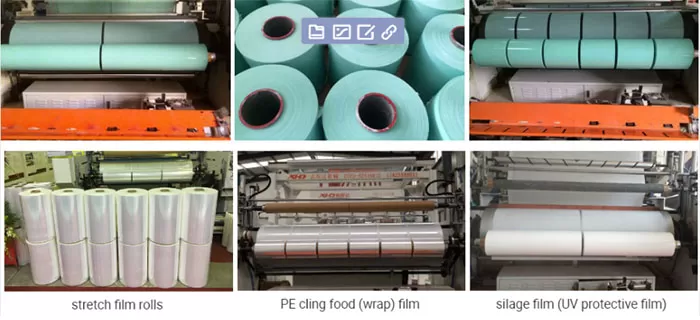
Brief information of the machine:
No. | Item | Description |
-
| Model: | XHD-65/90/65-1250 |
-
| Industrial Power Supply: | 3 phases industrial power supply |
-
| Total Installation Power: | 190 KW (for the machine only) |
-
| Main Raw Material: | LLDPE, LDPE (few) & MLLDPE |
-
| Thickness of Film: | 12-50 μm |
-
| Width of the Useful Film: | Maximum width 1500 mm |
-
| Film Layer Structure: | CBA three layers or CABAC five layers |
-
| Designed Linear Speed: | 200 M/min |
-
| Extrusion Output: | 150-280 Kg/H |
-
| Dimensions (L×W×H): | 14×5.5×4.6 M (for reference only) |
-
| Gross Weight: | 16000 Kg (for reference only) |
Highlights on machine performances:
1. High speed design: up to 200 M/min.
2. High working speed: 140~160 M/min.
3. High production capacity: 250~275 KGS/H (depends on the film thickness and line speeds).
4. Quality stretch film which can compare with the film produced by European machines.
5. Excellent production capacity and power consumption ratio: around 0.4 KWH/KG.
6. One man is enough to manipulate the whole machine!
7. Automatic paper cores unloading, finished rolls unloading, standby air shaft loading.
***Remarks: we also have the winder design for the jumbo rolls (up to 50 KGS per roll at 500 mm film width).
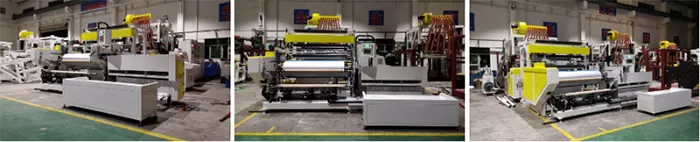
Stretch film machine and silage film machine bought by our Mexican customer.
Highlights on machine configuration:
(1) Coupling with rubber type of element is used to connect the main motor and the gear box.
(2) Alloy screws and barrels with good nitrogen treatment.
(3) Automatic screen changers powered by hydraulic station.
(4) Top quality XHD T-die (standard) or JC-TIMES T-die (optional).
(5) Big diameter (standard 720 mm/optional 800 mm) and quality cooling roller from professional suppliers.
(6) Silicone-coated roller is installed for cleaning the primary cooling roller.
(7) Synchronous wheels and belts, idle rollers with hardened surface are used for high speed production.
(8) Automatic air shaft inflation and deflation, automatic spare air shaft loading.
(9) Powerful crusher and new hopper design for recycled flakes feeding.
(10) Patented automatic system for paper cores unloading and loading.